Рост уровня механизации работ по добыче угля и последующей его переработки приводит к увеличению доли мелких классов и минеральных примесей в добываемой массе. На сегодняшний день переработка угольных шламов является одной из проблем углеобогащения, обострению которой способствовала неспособность традиционных технологий обеспечить необходимые показатели эффективности разделения материала. Дело в том, что тонкие классы имеют низкую селективность и именно этот фактор влияет на показатели эффективности обогащения угля. Это предопределяет повышение роли углеобогащения мелких и тонких классов вообще.
Что же собой представляют шламы? Шламы, как правило, — это углесодержащие продукты крупностью менее 0.5–1 мм. В свою очередь, продукты крупностью более 50 … 60 мкм — зернистые шламы, а класс крупностью менее 50 … 60 мкм — тонкие. По месту образования шламы различают первичные и вторичные. Первичные шламы поступают на фабрику с рядовым углем, вторичные — образуются в процессе обогащения. Находиться шламы могут в необогащенном виде, обогащенном и в виде отходов. Необогащенные шламы — это рядовые шламы. К обогащенным шламам принадлежат концентраты флотации, гидроциклонов, концентрационных столов, шламовых отсадочных машин, винтовых сепараторов и т.п. И как уже было сказано, шламы могут быть в виде отходов той же флотации, гидроциклонов, концентрационных столов и винтовых сепараторов. В рядовом угле и продуктах углеобогащения шламы составляют технологически значимую долю, которая имеет тенденции к росту. А значит потенциальному росту подлежит и осложнения обогащения, осаждения, сгущения, обезвоживания за счет изменения свойств суспензии шламами [4].
Согласно существующим данным, содержание в рядовом угле классов крупности 1 мм достигает примерно 20%. Суммарный выход вторичных шламов на некоторых углеобогатительных фабриках составляет 25–30%, а в отходах (флотации) содержание шламов может достигать 67–90%. В общем, в большинстве случаев содержание шламов может достигать 80–90%.При таких условиях наличие в технологической схеме эффективной технологии переработки шламов становится решающим условием стабильной и качественной работы фабрик.
Сейчас значительная часть шламов подлежит переработке пенной флотацией. Но недостатком этой технологии является ее низкая эффективность при повышенном содержании в исходном питании тонких частиц крупностью менее 50 мкм. Это способствует ухудшению качества как концентрата, так и отходов. Альтернативой этой технологии может выступать селективное обогащение угольных шламов маслами.
Содержание и технология разработки финансовых бюджетов
... сделать отбор методов финансового планирования; ознакомиться с технологией организации финансового планирования и бюджетирования на отечественных предприятиях; исследовать методики разработки операционных ... организации. 1.2. Принципы финансового планирования Они определяют характер и содержание плановой деятельности предприятия: принцип единства, координация планов отдельных подразделений, ...
Цель работы
Целью работы является повышение показателей качества угольного тонкодисперсного материала с помощью внедрения в технологическую схему обогащения технологии селективной флокуляции. В работе будут также раскрыты и доказаны как теоретически, так и практически преимущества обогащения угольных шламов маслами.
Традиционные методы обогащения шламов
На отечественных углефабриках обогащение угольного материала шламовой крупности зачастую осуществляется флотацией, которой подлежит 30ndash;40% шламов коксующегося и энергетического угля зольностью от 14 до 53% (в среднем 26%).
Но в ряде случаев пенная флотация не обеспечивает необходимого качества продуктов из-за недостаточной селективности разделения органической и минеральной составляющей обогащаемого угля, что объясняется наличием в шламе большого количества тонкодисперсных высокозольный фракций крупностью менее 40ndash;50 мкм. Это предполагает поглощение значительного количества флотационных реагентов и регуляторов среды, препятствование флотации более крупных частиц и возникновения большого количества стойкой пены, снижающей скорость флотации и уменьшающей производительность флотационных машин. В результате снижения селективности процесса флотации часть дефицитной органической массы угля теряется с отходами. Относительно высокое содержание в отходах органической массы не только приводит к потерям ценного коксующегося угля, но и затрудняет использование флотоотходов для производства строительных материалов.
Среди гравитационных способов обогащения шламов следует отметить тяжелосредные гидроциклоны, использование которых преимущественно распространяется. Но они обеспечивают высокое качество разделения полезных ископаемых только крупностью более 0,2–0,5 мм и поэтому применяются только исключительно для обогащения крупнозернистых шламов. Несмотря на ряд попыток сегодня, решить проблему эффективного обогащения тонких шламов с помощью тяжелосредных гидроциклонов не получается.
Не обеспечивают высокого качества разделения тонкого угля и другие методы гравитационного обогащения. Минимальная величина обогащаемого материала составляет: специализированные шламовые отсадочной машины mdash; 0,074 мм, концентрационные столы mdash; 0,074 мм, гидрокласификация mdash; 0,074 мм, винтовые сепараторы mdash; 0,045 мм. Причиной этого является, в частности, малые скорости перемещения частиц ила в условиях повышенной вязкости тонкодисперсных взвесей.
Сегодня делаются попытки замены флотации интенсивным технологиям на основе гравитационного разделения и гидрокласификации в зарубежных аппаратах типа «гидросайзер». Но эффективность их работы также резко снижается при повышенном содержании в исходном материале ультратонких иловых фракций.
Среди существующих технологий обогащения шламов следует уделить внимание масляной грануляции (агломерации).
Она принадлежит к нетрадиционным методам обогащения угольных шламов и несмотря на это хорошо изученным и эффективным процессом. В общем случае суть метода заключается в выборочной агрегации гидрофобных угольных частиц в водоугольной гидросмеси аполярним углеводородным связующим (маслом) в относительно прочные углемасляные агрегаты (агломераты, гранулы).
ДИПЛОМНЫЙ ПРОЕКТ/РАБОТА Тема работы Обогащение углей обогатительной ...
... обогащение в тяжелых средах (жидкостях и суспензиях); отсадка; обогащение в струе воды, текущей по наклонной плоскости (концентрационные столы); обогащение в центробежном поле; противоточная сепарация и др. Рисунок 1 – Классификация методов и процессов обогащения углей. ... ископаемых. В углеобогащении распространен метод пенной флотации, когда гидрофобная частица угля, прилипая к вводимым в пульпу ...
При этом гидрофильные минеральные частицы, которые не смачиваются маслом, остаются в водной фазе гидросмеси в диспергированном состоянии [6].
Процесс масляной грануляции обеспечивает обогащение и обезвоживание угольных фракций крупностью 0–0,5(1) мм. При этом одно из важнейших преимуществ масляной грануляции (агломерации) — возможность эффективной переработки угольных фракций крупностью 0–100 мкм. Серьезным недостатком, сдерживающим внедрение технологии масляной грануляции, являются высокие удельные затраты связующего углеводородного реагента (от 10–15% до 25–30% на сухую массу исходного угля), которым служат дефицитные в Украине углеводороды нефтяного происхождения mdash; мазут, печное и дизельное топливо, нефтяной пек и т.п. Кроме того, применение большого количества связующего неминуемо ведет к их частичной потере как с отходами грануляции, так и с водной фазой суспензии, что, в свою очередь, создает проблему загрязнения углеводородами окружающей среды. А также масляная грануляция имеет ряд специфических недостатков при обогащении тонкодисперсного высокозольного угля из суспензий малой плотности (100–300 кг/м3), которые ограничивают возможности использования технологии масляной грануляции для обогащения и обезвоживания целого ряда продуктов — отходов флотации угля, фугат центрифуг, шламовых вод mdash; характерных низким содержанием в суспензии тонкодисперсной и высокозольного твердой фазы.
Сегодня, в условиях недостаточной эффективности традиционных технологий обогащения и обезвоживания тонкодисперсного угля, а также дефицита и дороговизны реагентов, которые применяются в специальных технологиях (пример — масляная грануляция) на первый план выдвигаются процессы, которые, с одной стороны, обеспечивают значительное снижение затрат реагентов, а с другой — повышение селективности разделения тонких фракций. В этой связи перспективными представляются технологии, которые получили название селективной флокуляции.
Селективная флокуляции — перспективная технология обогащения тонкодисперсного угля
Итак, к перспективным технологиям обогащения принадлежат технологии под названием «селективная флокуляция», которая по сравнению с существующими технологиями переработки шламов является более эффективной и экономичной.
Селективная флокуляция — совокупность процессов выборочной агрегации тонкодисперсных частиц полезных ископаемых в микрофлокулы крупностью 100–300 мкм с помощью реагентов–флокулянтов различной природы. Последние, как правило, вводятся в водные дисперсии перерабатываемого тонкодисперсного материала, которые подвергаются интенсивной агитации в турбулентном режиме перемешивания гидросмеси. В турбулентных потоках суспензии протекает выборочное закрепление флокулянта на поверхности частиц определенной природы с последующим их связыванием за счет флокулянта в пухленькие пространственные структуры — микрофлокулы. При этом решающее значение приобретает степень родства флокулянта и поверхности частиц. Отделение сфлокулированного продукта от диспергированных частиц может осуществляться гравитационным, флотационных или магнитным методом.
Селективная флокуляции является универсальным процессом и может применяться для различных видов полезных ископаемых: руд черных металлов (особенно, марганцевых), оксидов и сульфидов цветных металлов, шламов редких металлов, золотоносных песков, шламов нерудного сырья. В зависимости от вида применяемого реагента можно выделить четыре основные разновидности процессов селективной флокуляции угля — неорганическими электролитами, маслами, водорастворимыми и гидрофобными полимерными соединениями. Вид реагента оказывает решающее влияние на результаты процесса, поскольку определяет механизм агрегатообразования. Подробнее рассмотрим селективную флокуляцию угольних шламов маслами.
Организация и технология процесса научного исследования
... оптимальная методика исследования. Нет методики исследования вообще, а есть конкретные методики исследования различных объектов, явлений, процессов, что придает каждому отдельному исследованию ярко выраженные ... опровергается, и тогда строится новая гипотеза и процесс исследования продолжается. 1.6 Составление плана научного исследования Выдвижением и обоснованием исходной гипотезы фактически ...
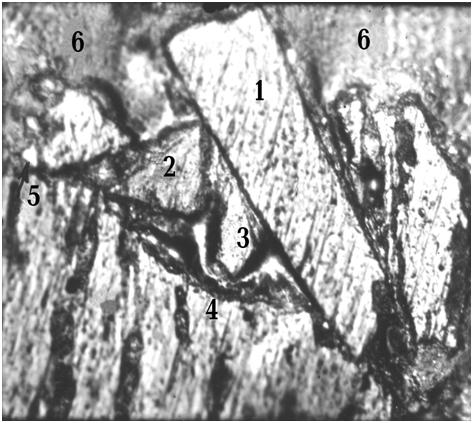
Большой интерес представляют собой разновидности технологий селективной флокуляции с использованием в качестве флокулянтов масел. Как уже отмечалось, высокие расходы связывающему и продолжительности турбулентного перемешивания в процессах масляной грануляции диктуются необходимостью получения гранулированного продукта определенной крупности (1,5–2 мм), что обеспечивает его эффективное выделение с минерализованной суспензии на стационарных ситах. Если отказаться от получения крупных и крепких гранул, то при наличии достаточно эффективного способа выделения мелких агрегатов (флокул), создаются условия для резкого сокращения продолжительности процесса, так и расходов реагента. Именно этим путем пошли авторы [2,3], предложив новый вид процесса селективной флокуляции ОВЗУМС — «обогащение высокозольных углей масляной селекцией». Суть метода заключается в высокоскоростной агрегации угольных частиц в микрофлокули (0,2–0,3 мм) в течение 0,5–3 минут турбулентного перемешивания водоугольной суспензии с масляным реаґентом. Отделение сфлокулированного продукта может осуществляться либо за счет аэроэфекта в камере флотомашини, или в центробежном поле осадительной центрифуги. Возможно сочетание масляной селекции с последующей грануляцией сфлокулированного продукта за счет дополнительной порции масла-связующего в количестве 10–15% от массы твердого. Технология отличается низкими затратами флокулянта-масла (0,5–2%) и высокой селективностью разделения. Область ее применения — обогащение и обезвоживания угля, в основном высокозольных (до 50–70%), тонкодисперсного (50–70 мкм и менее) угольного шлама из суспензий малой плотности (1–10 масс.% твердого), которые принадлежат к тяжелообогащаемым.
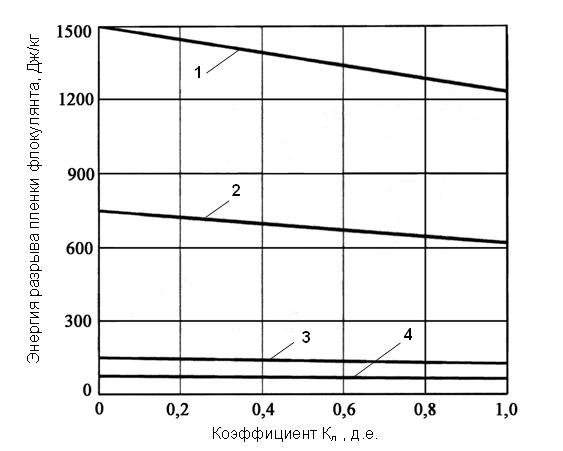
Аналоги процесса ОВЗУМС, разработанные в ряде исследовательских центров Германии, Великобритании, США, Канады, Японии и других стран. Некоторые разновидности процессов «Конвертоль»[4,5], «Олифлок»[6–8], NRCC [9–11] имеют относительно небольшие расходы связующего вещества (до 5%) и по своим признакам могут считаться прототипами селективной масляной флокуляции. Впервые селективная масляная флокуляция использована как субпроцес в индийском варианте технологии, названной «масленица агломерация» (МА).
Разработка технологии процесса изготовления отливки
... и стержней, способствовать направленному затвердеванию. Обычно, при проектировании литейной технологии для конкретной отливки возможны несколько вариантов положения отливки в форме и ... приведена схема технологического процесса изготовления отливки “ступица". Рисунок 1.1 - Схема технологического процесса изготовления отливки "ступица" 1.3 Оценка технологичности отливки Технологичность данной детали ...
Эта технология разработана в 70–х годах в Центральном исследовательском институте топлив Индии (Central Fuel Research Institute, Д.Саркар, Бхаттачачья и др.) [12].
Основные этапы процесса МА такие:
1. Селективная флокуляция, которая иногда совмещается с мокрым измельчением в мельнице. Как реагент применяется легкое масло в количестве 0,5–3 мас.%.
2. Агломерация угля в суспензии високовязким связующим при его расходах 5–10 масс.% и его выделение на грохоте. Окомкования гранулята на тарелчатом или барабанном аппарате–окускования.
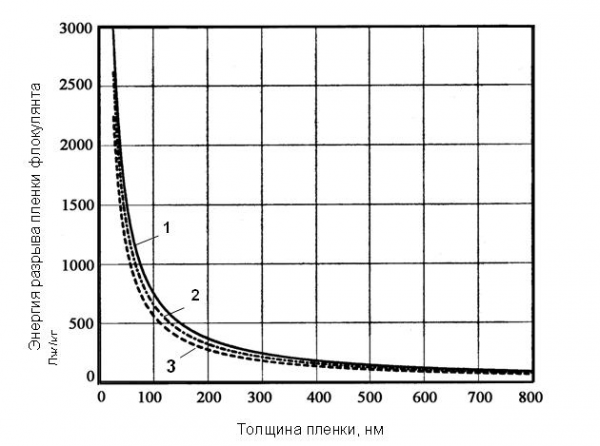
В первом варианте технологии как реагент на стадии селективной флокуляции применялось дизельное топливо, как високовязкое связующее — высококипящие фракции масел. При флокуляции фактор рН регулировался кислотой или щелочью в пределах рН = 5–9. Для коксующегося угля поддерживалось слабощелочную среду, для энергетического — кислую. Продолжительность совмещенного процесса измельчения–флокуляция» составляла 0,5–1,5 ч., продолжительность агломерации — 3 мин. При зольности исходного угля А d = 12–40% получали гранулированный концентрат зольностью Аd =5–21% и отходы Аd = 60–85%.
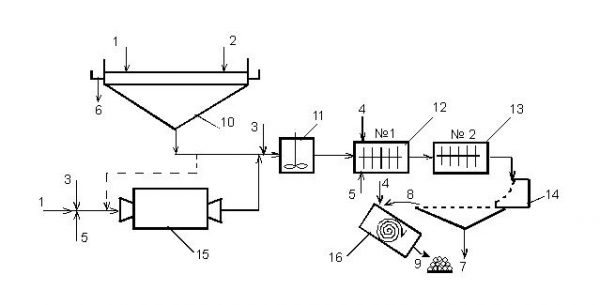
Этот вариант технологии было реализовано компанией «Бхарат Коукинг Коул ЛТД» (Лодна, Индия) на полупромышленной установке производительностью 2 т/ч (рис.4).
Исходное угля сначала направляли на мокрое измельчение и масленицу флокуляцию в слойной мельница и (или) контактном чане. Суспензию сфлокулированного угля разбавляли водой, вводили високовязкое масло и полученную смесь последовательно перемешивали в двух горизонтальных грануляторах при пв1=400 мин -1 и пв2=600 мин-1 . Полученный агломерат обезвоживали на дуговой сити, а затем на виброгрохоте. Агломерат подвергали образование комков со связующим на тарелчатом ґрануляторе сухого типа. Исходный материал — уголь крупностью 0–0,1 мм и угольные шламы крупностью 0–0,5 мм. Расходы низкокипящего (дизельного) масла на этапе масляной флокуляции составляли 1–2 масс.%, высококипящего (креозот, печного масла) на этапе агломерации — 10–18 масс.%. Регулятор среды, луг, дозировался в суспензию на стадии флокуляции. После разбавления водой концентрация взвеси снижалась с 35–40% до 15–20%. Продолжительность агломерации –3–8 мин. При зольности выходного Аd =17–41% характеристики продуктов аґломерации были такие: зольность агломерата Аd =9–22%; величина dа=2–8 мм; влажность W =10%; зольность отходов масляной агломерации Аd =62–71% [13,14].
Установка селективной очистки масел
... и имеет более светлый оттенок цвета. На нефтеперерабатывающих заводах топливно-масляного профиля установка селективной очистки может находиться в составе маслоблока. .1 Общая характеристика ... производственного объекта Установка селективной очистки масел 37/1 предназначена для удаления из масляных фракций смолистых веществ, полициклических ароматических и нафтено- ...
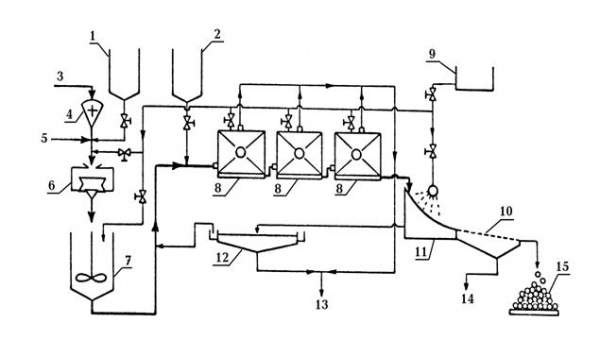
Во втором варианте технологии (рис.5) исходный углоль подвергали селективной масляной флокуляции в коллоидной мельнице на протяжении 1–2 мин, затем суспензию разбавляли водой, вводили високовязкое связующее и выполняли аґломерациюю в флотокамере без подачи воздуха. Полученный агломерат обезвоживали на дуговом сите и виброгрохоте или на дуговом сите и в смеси с углем крупностью 0,5 мм — на фильтрующей центрифуге. Агломерат знемаслювали термическим способом при 300С. Реагент–флокулянт — дизельное масло или газойль при затратах 0,5–3 мас.%. Связующее для агломерации — печное или антраценовое масло при Qм = 8–12 масс.%. Плотность суспензии на стадии флокуляции тележки Рвс1=35–40%, аґломерации Рвс2=15–20%. Частота вращения импелера флотомашини пв=1300 мин-1. При крупности исходного соответствующего угля 0-0,1 мм и его зольности 17-40% получали агломерированный концентрат зольностью А=10–21%, крупностью dа=2 мм, влажностью W =7%. Зольность отходов составляла А=58-77%.
По сути индийский вариант технологии являются одним из первых ярких примеров реализации масляной флокуляции тонкого угля, хотя она и использована как составной процесс селективной масляной агрегации.
Масляная флотация — процесс селективной флокуляции угля с последующей флотацией флокулянта. Способ предназначено для обогащения и обезвоживания угля крупностью 0–1 мм. Согласно нему водоугольная пульпа плотностью 35–40 % твердой фазы класса 0–0,5(1) мм смешивается со смесью парафинового и дегтевого масла в пропорции в соответствии 1–1,5 мас.% + 0,05–0,2 мас.% от сухого угля. Пульпа с реагентами перемешивается в турбулентном режиме, углемаслянний флокулят удаляется флотацией без добавки дополнительных реагентов и потом обезвоживается в центрифугах.
Процесс «Aglofloat» предусматривает селективную флокуляцию или агломерацию тонкодисперсного материала с последующим удалением флокуляту (аґломерату) флотацией. Разработанный в конце 90–х годов он апробирован для очистки омаслених грунтов, а также для сероочистки угля. В последнем случае переработке подвергается угля крупностью 0–0,6 мм. Расходы масляного реагента составляют 0,5 — 5 мас.% от сухого угля. Продолжительность агитации пульпы 30–60 с. Концентрация пульпы — 10 % твердой фазы.
Испытания процесса на суббитуминозном угле рудников штата Монтана показывает, что при использовании смеси битума и тяжелой нефти (Qм = 5 мас.%) процесс «Aglofloat» обеспечивает уменьшение содержания серы в угле с 4,4 % до 1,8 %. При этом удаляется около 95 % неорганической (пиритной) серы.
Химизм процесса пиролиза
... и может увеличивать скорость науглероживания радиантных труб. 1.2Факторы влияющие на процесс пиролиза На процесс пиролиза влияют следующие основные факторы: 1. температура 2. время контакта ... освоено производство хлорвинила и поливинилхлорида. 1. Теоретические основы процесса пиролиза Пиролиз - процесс высокотемпературного разложения углеводородного сырья, протекающий при температурах свыше 600° С. ...
Селективная флокуляция маслами удачно сочетает преимущества как масляной ґрануляции (высокая селективность разделения, возможность переработки тонкодисперсных фракций крупностью менее 40–50 мкм), так и пенной флотации (выделение концентрата за счет аэроэфекта).
Благодаря этому она в ряде случаев может эффективно конкурировать с флотацией и с «классической» масляной ґрануляцией Более того, в случае переработки высокозольного угля из суспензий малой плотности она становится единственным достаточно эффективным способом обогащения.

Выводы
Укажем, что из всей совокупности возможных путей повышения эфективности перерработки тонкодисперсних угольних шламов наболее перспективными сегодня являются технологии селективной флокуляции гидрофобными реагентами, в частности, маслами и синтетическими латексами и их аналогами.
Важное замечание
При написании данного автореферата магистерская работа еще не завершена. Окончательное завершение: декабрь 2011. Полный текст работи и материалы по теме могут быть получены у автора или его руководителя после указанной даты.
Литература
[Электронный ресурс]//URL: https://inzhpro.ru/referat/maslyanaya-flotatsiya/
- Елишевич А.Т., Белецкий В.С., Сергеев П.В. Обогащение и обезвоживание углесодержащих продуктов методом масляной селекции// Обогащение полезных ископаемых.– Киев: Техніка, 1988.–вып.38.– С.63–66.
- Polymeric Flocculants / Kristian S.V., Attia Y.A. // Reagents Miner Technol.– New York. Basel, 1988.– p. 485–518.
- Небера В.П. Флокуляция минеральных суспензий.– М.: Недра, 1983.– 288 с.
- Мнушкин И.Н. Исследование процеса селективной коагуляции угольных шламов.Автореф.дисерт.на соиск.учен.степ.канд.техн.наук.–Днепропетровск 1973.– 23 с.
- Байченко А.А. Научные основы и интенсивная технология очистки шламовых вод углеобогащения. Автореф. диссерт. на соиск. учен. степ. докт. техн.наук.– М.: 1987.– 34с
- Lakatos I. Flocculation of Coal Sludges by polyacrylamides // Publ. Techn. Univ. Heavy Ind.– 1986. A42. – № 1–4.
- Porookes G.F., Littlefair M.I., Spenser I. Селективна флокуляція вугільносланцевої суспензії з використанням звичайних і модифікованих полімерних флокулянтів // Worldwide and Appl. Miner. Process Technol., Toronto, Oct. 17–23, 1982, p. 7–8.
- Spenser L., Thompson S., Brokes G.F. Hydrophobic polymers in coal preparation. “MINPREP 87”: Symp. and Exhib. Innov. Plant and Process. Miner Eng.,Donkaster 31 March – 2 Apr., 1987. Liffleover. 1987, p. 173–189.
- Нейман Р.Э., Киселева О.Г., Егоров А.К., Васильева Т.М. Коллоидная химия синтетических латексов.– Воронеж: Изд–во ВГУ,1984.– 196 с.
- Лебедев А.В. Коллоидная химия синтетических латексов. – Л.: Химия, 1976.– 100 с.
- Никитин И.Н. Разработка флокуляционно–флотационного способа обогащения угольных шламов с применением латексного флокулянта. Автореф. дисссерт. на соиск. ученой степ. канд. техн. наук . – Люберцы; ИОТТ,1986 .– 16с.
- Никитин И.Н. Флокуляционно–флотационный способ обогащения угольных шламов //Уголь.– 1992.–№ 3.– С.49–51.
- Сергеев П.В. Разработка и внедрение технологии обогащения высокозольных угольных шламов методом масляной селекци. Диссертация на соиск. ученой степ.канд.техн.наук. – Донецк: 1992. – 173 с.14
- Киселев А.В, Древинг В.П. Экспериментальные методы в адсорбции и молекулярной хроматографии.– М.: Изд–во МГУ, 1973. – 448 с.
- Богеншнейдер Б., Беренбек А., Кубитца К. Обогащение тонких угольных шламов методом селективной агломерации // Глюкауф.– 1976.– № 23, С.19–25.
- Lemke K. Sortierung und Entwasserung von Schlam nach dem Convertol verfahren // Gluckauf – № 39/40, 1954. – S. 219–224
- Lemke K. Wege und Ziele der Entwasserung von Fein– und Feinstkorn beider Aufbereitung von Steinkohle// Gluckauf – № 17\18, 1956 – S. 452-465.
- Кейпс К.Е., Мак Иллини, Мак Кивер. Применение сферической агломерации в углеобогащении// 7 Международный конгресс по обогащению углей. Сидней, 1976. – Н2.
- Chen C.H., Nguyen G.V. Cleaning a Western Canadian coals by spherical agglomeration//Proc. 73rd Annu. Meet., Montreal., 1980. – V.1, p. 22–27
- Mehrotra V.P., Sastry K.V.S., Morey B.W. Review of oil agglomeration techniques for processing of fine coals// Int. J. Miner. Process. – 1983. – 11, №, p. 175–201.
- Деминерализация углей с помощью технологии агломерации / Саркар Д.Д., Конар Б.Б., Сакха С., Синха А.Р.// 7 Международный конгресс по обогащению угля. Сидней. 1976. – Н3.
- Эффективное обогащение труднообогатимых углей с применением отсадки и масляной агломерации/ Конар Б.Б., Саркар Д.Д., Рао Т.К. и др.// Технические документы 9 Международного конгресса по обогащению угля. – Нью Дели, – Н3.
- Исследовать процесс обогащения угольных шламов с использованием органических соединений на установке «МогифлокRaquo;: Отчет о НИР(Заключительный)/ ИОТТ. рук. М.А.Борц. – № ГР 01840068107. инв7 № 2984/2. – М., 1984. – 89
- Патент Англії 8504787. М.кл. В 03 D 1/02. Method for recovering fine granulated coal by flotation / Murata Toshiaki. – Заявл. 25.02.85. Опубл. 28.08.86.
- Патент Англії 1575413. М.Кл. G 10L 5/10. Метод аґломерації тонких класів вугілля / М.Д.Кеннон, Е.Д.Клейфілд, О.Піннінгтон, П.Сент. – Заявл. 1976. Опубл. 1980.
Обзор конструкций центрифуг, применяемых для обезвоживания угольных ...
... в герметичную оболочку; 9)специальное — для работы в специальных условиях. Обезвоживание концентратов и промежуточных продуктов гравитационного обогащения на фильтрующих центрифугах Цель данной операции – разделение исходного материала ... Фугат осадительной секции направляется, как правило, на сгущение вместе с тонкими шламами. Фугат фильтрующей секции, содержащий более крупные частицы и имеющий на ...